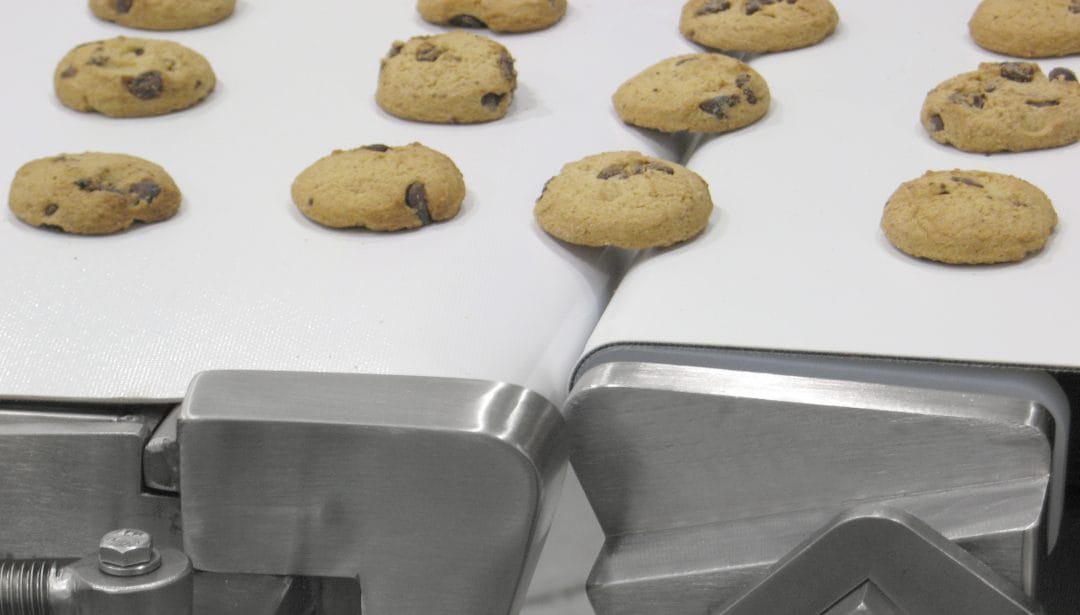
Effective product transfers ensure quality, efficiency, and safety in any production line. Whether a product needs to be transferred from one conveyor line to another or from machine to conveyor and onto the next processing step, designing the transfer method around your product and operation is critical to reducing waste, backups, and downtime.
The transfer method can vary widely depending on the product and process being performed. We’ll review the five main transfer options available, discuss their pros and cons, and show which application they are best suited for.
1. Inline Transfer
Also called an end-to-end transfer, this method is when the roller or drive end of a conveyor butts up against the next conveyor, forming a straight line from one belt to the next. While this is one of the most straightforward transfers, it still requires careful planning to ensure both conveyor profiles match to reduce the potential for the product to fall between the two conveyors.
In an inline transfer, there is typically a small gap between the two conveyor ends, so this method may not be ideal for tiny or flexible parts that may fall through the space. That said, Dorner’s low-profile conveyors close the gap in end-to-end transfers to as little as 1.25 inches.
This transfer method is a great, cost-effective option for transferring parts between lines or from machine to conveyor line as it does not require additional parts or accessories. Inline transfers are ideal for industrial applications, as well as in logistics and warehousing operations.
Pros:
- Greatest cost savings
- Space saving
- Handles a wide range of product sizes and shapes
- Simple to configure
- No additional parts required
Cons:
- There is a small gap between conveyors
- Conveyors must match profiles to transfer products effectively
- It is not ideal for very small products or parts
2. Transfer Plates & Rollers
Transfer plates are flat metal plates installed in the gap between conveyors and are a cost-effective way to eliminate the gap between conveyors for a smoother transfer. A similar option is a roller plate, which incorporates rollers in a frame to reduce the friction on products as they transfer from one conveyor to another. These are great for large-scale or bulk production lines that process small products such as bottles and cans. Typically, these processes involve some backpressure from other products on the line, so there is no need for a powered transfer to maintain product momentum through the transfer.
Pros:
- Simple and cost-effective method of bridging gap between conveyors
- Ideal option for products with low stability
- Fits with most conveyor systems
Cons:
- Guiding is recommended to ensure no product loss during transfer
- Not ideal for low-capacity production lines
3. Nose Bar Transfer
Similar to the Inline transfer, a nose bar transfer also aligns two conveyors end-to-end, but one (or both) ends of the conveyor are replaced with a small diameter end roller and lower profile supports. This allows conveyors to sit closer together without interfering with their function and reduces the gap between ends to as little as 0.31 inches.
The nose bar transfer method is ideal for infeed and outfeed transfers from machinery and unit handling within a machine. The nose bar allows for additional clearance around the end of the conveyor, making it more accessible and creating room for other machinery to be integrated. The tighter transfer space also means conveyors can smoothly handle small parts without risking product loss between the conveyors or damage during the transfer.
Pros:
- Ideal for small parts and product transfers
- Tightest transfer space
- Added clearance on roller end for easy machine integration
- Multiple options depending on application needs
Cons:
- Limited to certain types of belting and conveyor models
- Not recommended for high-speed applications
- Shorter required maintenance intervals
4. 90° Transfer
This type of transfer shifts the product perpendicularly from the end of one conveyor over the side of another. This transfer method, in particular, benefits from low profile or flush frame conveyors where there is as little frame as possible between the transferring conveyor end and the receiving belt. This transfer method is better for medium to larger-sized products or packages because the product will need to transfer over a small portion of the frame.
90° transfers offer a flexible and inexpensive solution for transporting products between conveyance lines as well as for configurations where lines must turn around machinery or working spaces. In applications where the belting or product cannot facilitate curved conveyors, 90° transfers provide smooth transitions and direction changes as needed.
Pros:
- A simple method for changing line direction
- Saves space and easily transports product around machinery
- Adapts to a wide variety of belting types
- Easily transfer product from multiple conveyor lines onto one
Cons:
- Product orientation is not maintained through transfer
- Only available on certain conveyor models
- Highest amount of friction between product and belt
5. Side Transfers
Side transfers are a unique option for sorting, accumulation, and positioning applications. This transfer method is configured with two conveyors running side by side, and guiding is used to gently push product from one conveyor to the other as the belt runs. This is a great way to move large quantities of product through multiple lines for sorting or to position products into lanes for the next step in production.
This solution is not meant for all conveyor types because the product moves across the belt edges at an angle. Side transfer conveyors must have little to no frame past the edge of the belt and are better suited for modular or flexible plastic chain belting, which offers the rigidity needed for this type of transfer.
Pros:
- Great for bulk product transfers and accumulation
- The product maintains momentum through the transfer
- Smoothly aligns products into lanes
- Transfers can be configured on curves
Cons:
- Requires added guiding and accessories
- Longest transfer module
- Not ideal for high-friction products
6. Powered Transfer Modules
The final method is powered transfers. This encompasses a variety of transfer modules that utilize electric controls, pneumatics, or powered rollers to transfer products from one conveyor to another. Some powered transfer modules require more programming than others. Pneumatic pushers, for example, rely on sensors to tell them when a product is in position for transfer. In contrast, powered rollers are a more straightforward module installed between conveyor ends and series driven to smoothly transfer products without losing speed. Powered transfer options are a great solution to maintain smooth product conveyance while taking up as little space as possible.
Powered transfers are best used for delicate or small products and in applications where products must maintain the same speed throughout the production line. This method is also perfect for adding automation to your production line, where products may need to change direction, maintain precise orientation, or move from one line to another without losing momentum.
Pros:
- Maintains product speed and orientation
- No gap between conveyors
- Space-saving solution
- Effective for heavy or high friction products
- Gently handles delicate products to reduce the potential for damage
Cons:
- The most expensive transfer option
- Some modules require added sensors and programming
- It is not ideal for bulk products to be transferred at once
Best in Class Product Transfers from Dorner
Conveyor transfers are frequently overlooked but vital to adequate product transportation. No matter the product or application, careful consideration of the best transfer method is critical to maintaining efficiency, quality, and safety. Dorner’s conveyor experts offer the industry’s best transfer options. They will work closely with you to develop a conveyor transfer method that meets both the requirements of your operation and products. We take the time to understand you and your product to design and build the ideal conveyance solutions to carry your business into the future.